April 13, 2020
Penn State team develops prototype for testing site protective booth
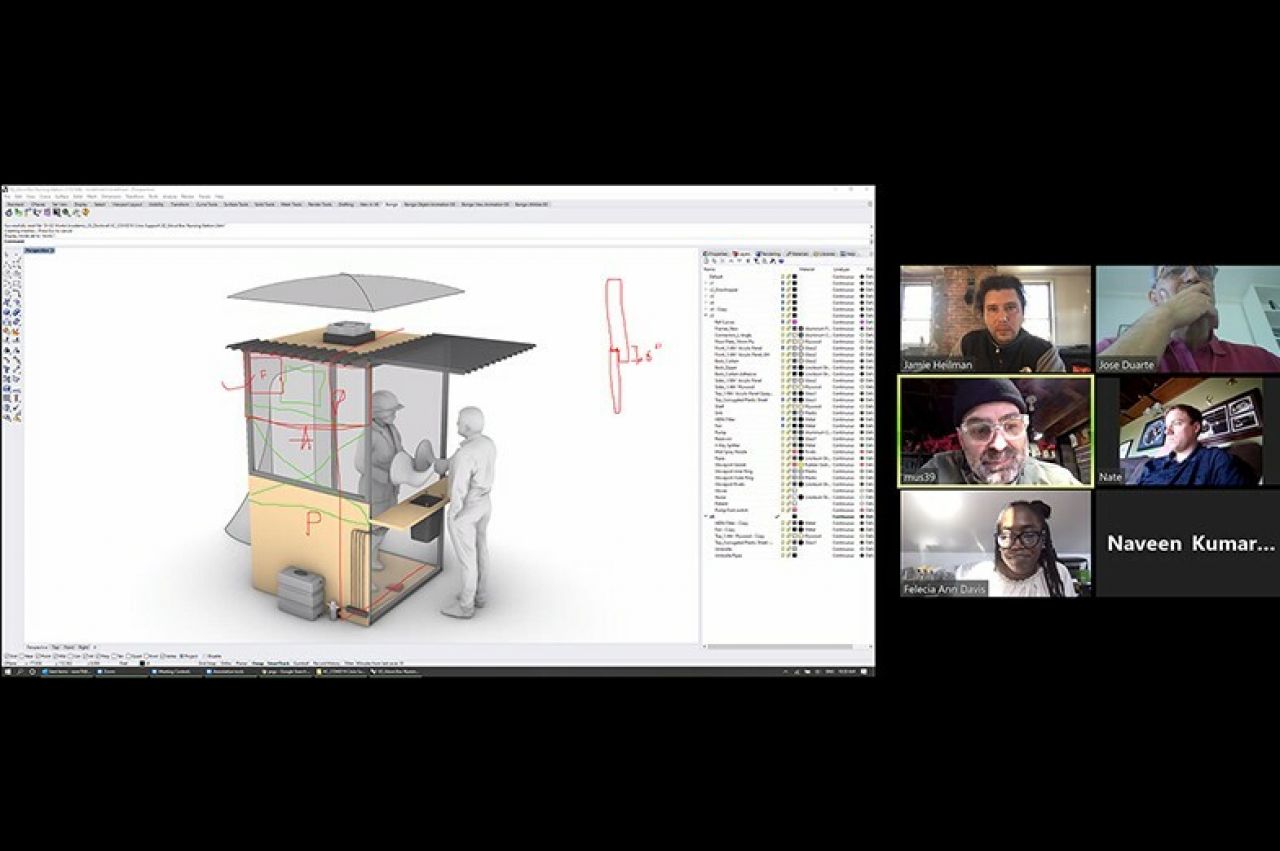
UNIVERSITY PARK, Pa. – A team of faculty, graduate students and staff from the Stuckeman School and the College of Engineering at Penn State have teamed up to design and build a “glove box nursing booth” prototype that could potentially be used by health care providers working at drive-thru COVID-19 testing sites.
It is well documented that the surge of COVID-19 cases across the country has led to an unprecedented shortage in personal protective equipment (PPE) for medical professionals on the front lines of the pandemic. Penn State has stepped up to address the shortage through the University-wide Manufacturing And Sterilization for COVID-19 (MASC) Initiative.
Researchers in the Stuckeman Center for Design Computing (SCDC) in the College of Arts and Architecture and the School of Engineering Design, Technology, and Professional Programs (SEDTAPP) are building off of that initiative by prototyping a nursing booth that is designed to allow health care employees working at drive-thru COVID-19 testing sites to safely collect samples from patients who may be infected with the coronavirus. The booth, which has been named the Barrier for Outside Outpatient Testing of Heath (BOOTH), could also eliminate the need for PPE – such as masks, gloves and gowns – as it provides a highly protective barrier between the provider and the patient. It also features a built-in sanitizing system.
José Pinto Duarte, director of the SCDC and the Stuckeman Chair in Design Innovation, served as the multidisciplinary team leader and said a similar testing booth developed by doctors at Brigham and Women’s Hospital in Boston was used as a reference. An initial proposal was designed by Naveen Muthumanickam, an architecture doctoral student, with assistance from Felecia Davis and Marcus Shaffer, both faculty members in the Department of Architecture; Jamie Heilman, digital fabrication and specialized technologies coordinator in the Stuckeman School; and Duarte.
The idea was to design and construct a scaled-up version of what engineers and scientists call a ‘reversible glovebox or isolation glovebox." – Naveen Muthumanickam
“Our version would need to accommodate a nurse who stands inside a booth and uses the reversible gloves to collect nasal swabs from patients outside the booth, thus preventing spread of the virus through contact.”
A number of important factors drove the design of the BOOTH, including the fit, the height and spacing of the arm holes and the need for the patient to remain in fresh air. Shaffer said the architects turned to a book on human factors called “Measure of Man,” which is a resource architecture faculty often reference with their students. The team also relied on the ergonomic expertise of Matthew Parkinson, director of the Learning Factory and professor of engineering design and mechanical engineering.
“In terms of the anthropometric information, selecting the correct data and using the information in a knowledgeable way by making some assumptions for the bodies that will occupy and use the testing booth were important to the overall design,” said Davis, who is the director of the Computational Textile Lab (SOFTLAB) in the SCDC.
The team also decided that completely sealing the booth and incorporating a device to automatically sanitize the gloves after each test were must-have features that were not part of the referenced booth.
Both Shaffer and Heilman have extensive backgrounds in fabrication and assembly and were able to inform Muthumanickam’s design in terms of material choices, portability and cost.
“In general, my role is to help students and faculty learn to use our school’s design and fabrication tools to bring their projects from ideas to physical objects,” said Heilman. “The BOOTH project is an exciting change of pace because this time I get to be involved in the entire process, from design meetings through fabricating a finished prototype. The fact that we are taking part in a massive effort within the University, the nation and the world, makes this work even more fulfilling.”
Standard parts for the frame – including lightweight aluminum, bolts, infill acrylic and plywood – were ordered from online vendors and shipped to Shaffer’s home, where he got to work.
“A big part of the design is the concept of employing ‘off the shelf’ materials – hardware and parts,” said Shaffer. “We can't spend time making parts from raw materials.”
Another factor that came into play is the needed ability to sanitize the BOOTH, which meant using materials such as aluminum, stainless steel, plastic and painted components that would stand up under sanitization without compromising the structure.
Shaffer constructed the structural frame and flooring for the test station – which measures 7 feet tall by 4 feet wide by 4 feet deep – using the tools and workspace in his garage.
While Shaffer was assembling the framework, Nate Watson, a master’s student in the Additive Manufacturing and Design program, was building the mechanical systems for the booth with remote guidance from Sven Bilén, head of SEDTAPP and professor of engineering design, electrical engineering and aerospace engineering. Watson was able to find all of the parts online with minimal custom fabrication needed and had them shipped to his home.
“The sanitizing mechanism feeds a sanitizing liquid from a reservoir through a pump, which distributes the liquid to four misting nozzles that are mounted in the corners of a plastic collection container,” explained Watson. “The nozzles are able to spray a thin but complete covering over the gloves to kill any potential viruses between users of the booth and the booth attendant is able to trigger the pump on and off using a foot pedal located inside of the booth.”
Since the team decided the BOOTH needs to be sealed completely in order to provide the most protection to health care workers, Watson also designed the system to regulate indoor air quality and temperature.
“Lack of access to our usual tools and prototyping facilities were probably the most challenging obstacles to overcome,” said Bilén. “Also, design is typically a fairly social process – and includes the building of physical prototypes together – but here, we had to be cognizant of social distancing guidelines.”
Once the framework and the electrical systems were complete, Shaffer and Watson staggered dropping their respective pieces off to a central collection site where Heilman got to work completing the structure.
According to Muthumanickam, designing the booth in a modular fashion, remotely and by different people, required the highest level of precision.
“The most challenging part was to coordinate such high-precision construction and fabrication details across multiple people working on various parts remotely,” he said. “There had to be little to no margin of error as even a small glitch, such as the wrong part being ordered or a simple assembly mistake being made, might take longer than usual to rectify due to [Gov. Tom Wolf’s ‘Stay-at-Home’] order and remote working conditions.”
The team relied on Skype, Microsoft Teams and Zoom for their design meetings, and cloud storage, like Box, for file and information exchanges. Advanced remote collaboration features, such as annotating a participant’s screen and being able to remotely control a participant’s screen, allowed the team to interactively modify the design during their review meetings.
While he missed the interaction of working through iterations in person with a team, Watson considers himself lucky to have been a part of this unique group effort.
“The whole project was very motivating, knowing that we were creating something that could help those on the front lines fighting for our own safety,” said Watson.
Once the prototype is tested, the team will be able to further tweak the design.
“We will be able to see if nurses should sit or stand, if the arms are placed in a comfortable way...as well as how much time nurses have in between doing tests that would inform the positing of their arms,” said Davis.
Duarte said he felt compelled to lead the project as both a researcher and a member of the community.
We all want to be safe and each of us has the moral obligation to contribute to this common goal whenever we can.” – José Duarte
“For most of us right now, this simply means complying with social distancing guidelines; however, as a research director at Penn State, it also means fulfilling the community outreach goal of the University so when the opportunity arose to help, I was immediately up for the challenge.”
Shaffer, who is also 3D printing face shields from his home, echoed Duarte’s thoughts and expanded on his own position.
“For many of us . . . design and architecture for populations in humanitarian crisis is a deep interest,” he said. “We are involved in architectural environments of scarcity and need – through our teaching, through the graduate students we advise and through our own research – but it is always at some distance because we are here, on a campus in the middle of Pennsylvania. But today, we are also that population, we are also in that environment; and luckily, we can respond, through our long-formed knowledge and through action.”
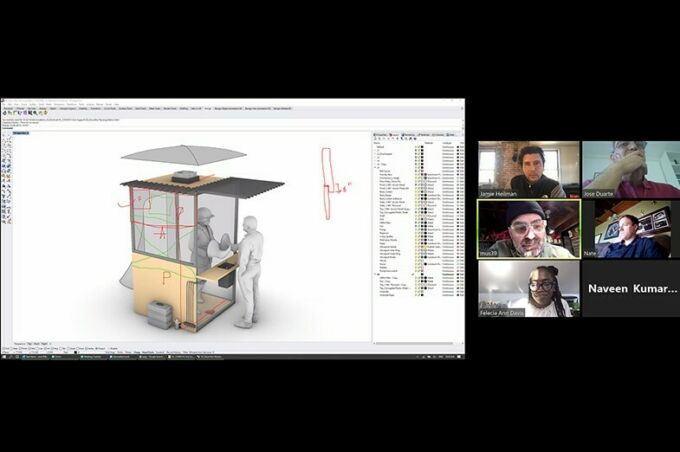
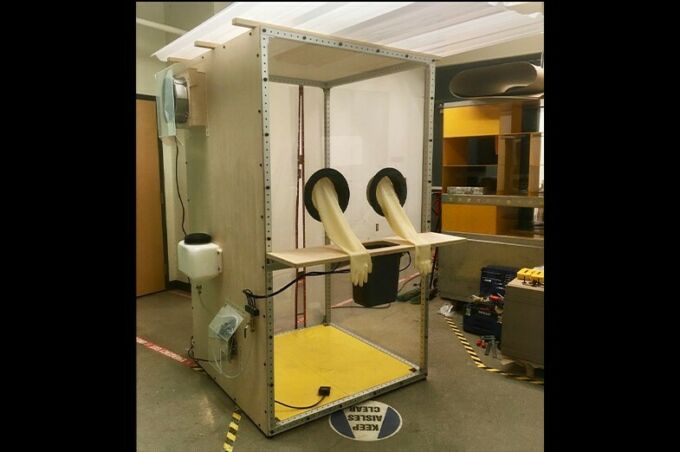
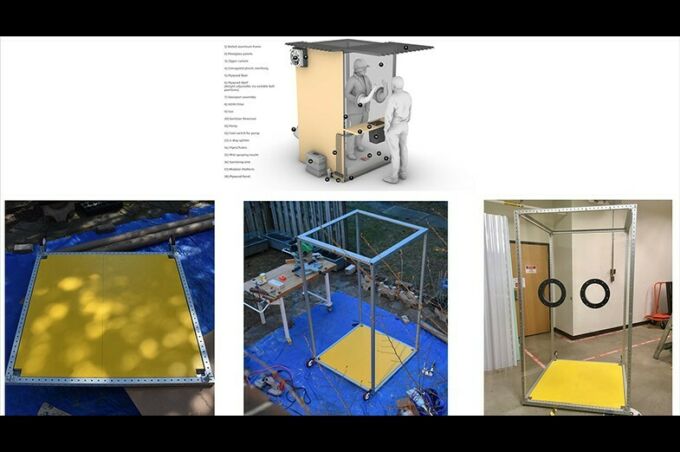
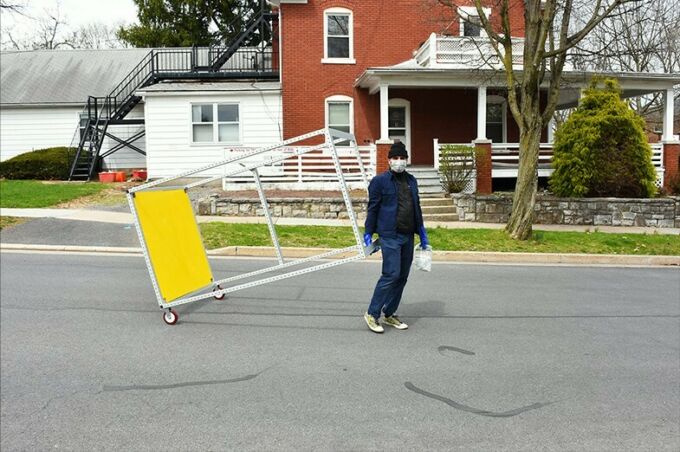